A story of soaring demand and rising challenges – REJournals
These are interesting times for commercial construction. Demand for new industrial facilities, multifamily properties, data centers and advanced-technology manufacturing spaces is soaring.
At the same time, developers and contractors face labor shortages and long delays for the building materials they need.
Anthony Johnson knows all about these highs and lows. He’s president and shareholder and industrial business unit leader for St. Louis-based real estate, construction and architecture firm Clayco. He understands just how unusual these times are.
Midwest Real Estate News recently spoke with Johnson about the state of the commercial construction industry. Here’s what he had to say.
Let’s start with the hottest sector: How strong is industrial in your home market of St. Louis?
Anthony Johnson: St. louis is a smaller industrial market, but going by a pro-rated set of standards, St. Louis has had some very strong years in industrial. We have seen strong development activity on the Missouri side of the St. Louis market. In fact, we just completed a couple of facilities for Amazon last year. There is also the portion of our market that extends to the eastern side of the river in Illinois. Right now, the largest spec warehouse building that has ever been constructed in this market is being developed on that side of the river by NorthPoint Development.
Why has industrial been so strong for so long?
Johnson: The reasons seem to be evolving on a near-daily basis. There has been a substantial change in consumer behavior when it comes to ecommerce. Online shopping became even more prevalent when the pandemic started, and as the pandemic extended, more people’s shopping habits changed. They became even more comfortable with buying more products online. That growth and demand came at the same time we saw so many challenges with the supply chain. This combination changed a lot of companies’ approaches to how they structured their supply chains, how much product they held close at hand. There has been an ongoing modification and evolution that exacerbated the growth in industrial demand.
Some of the shipping and supply chain issues that we saw with distribution also surfaced in the manufacturing world. Having product available domestically versus relying so heavily on having your products overseas became an important move for companies. The geopolitical issues that have been ongoing have also influenced the demand for more industrial space here. Earlier, we had the rapid Chinese shutdowns in response to COVID. Now we have the current situation in Ukraine and Russia.
Because of all this, a lot of companies are focused on onshoring their manufacturing. That, too, has driven a lot of demand in the industrial market. So it’s not just ecommerce, not just a need for more distribution space, but also the growth of manufacturing here that has contributed to industrial’s strength.
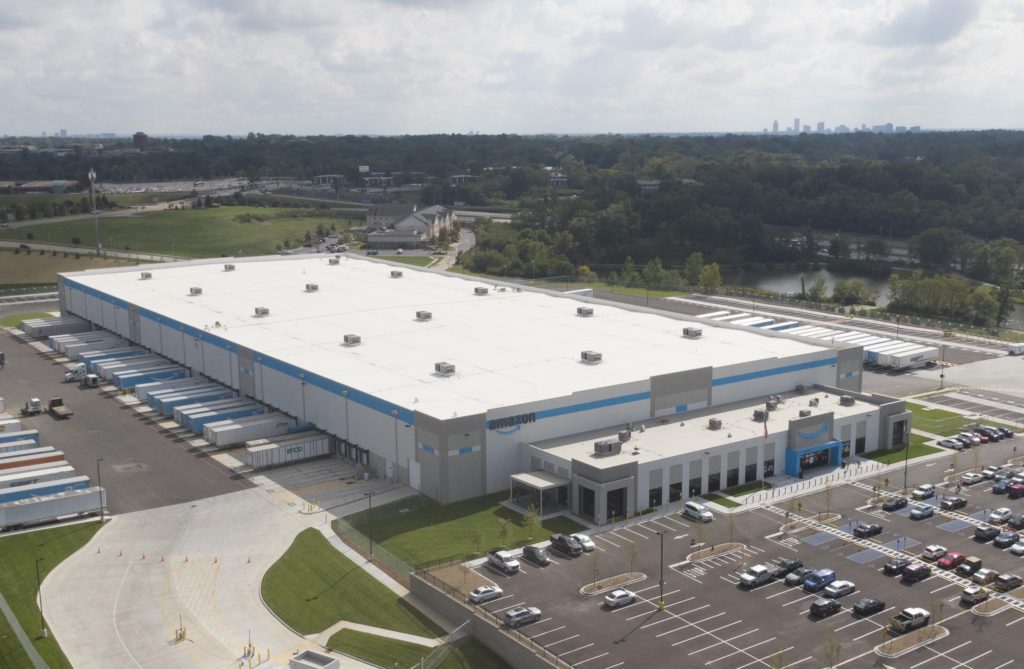
How challenging is it today, though, with the labor shortage and the longer time it is taking to get building supplies?
Johnson: Those concerns top of all our conversations internally. There is not a day that goes by where material procurement is not part of a conversation. The products change that are delayed, though, have changed over time. Initially it was steel. Then it was roofing products. For a while it was lumber. The biggest thing that has surfaced lately is electrical and mechanical equipment. There is a very large demand for that type of equipment with all the new builds. There is a large demand for mechanical and electrical systems that manufacturers haven’t been able to keep up with.
Then there are one-time events that cause supply chain issues. For instance, a copper bust production plant caught fire. Electrical gear uses copper busts. That exacerbated some supply chain issues. These challenges are not something that has gone away or is going away anytime soon. These challenges will continue into next year. We are going to have to continue to pivot quickly in reaction to these challenges. We’ll have to adjust our processes. We need to be in real-time dialogue with all our customers, contractors and suppliers to adjust schedules when needed.
The multifamily market has been strong, too, right?
Johnson: The market-rate apartment market is one that has a lot of momentum behind it, both in traditionally active markets like Chicago but then also in some of the markets that as people have transitioned to remote working they are looking to move into. Markets like Nashville, Charlotte and Phoenix are seeing strong demand for multifamily product.
Any other commercial sectors that are particularly strong right now?
Johnson: There is a strong demand for mission-critical data center construction. There has not been a slowdown in that market at all. As the pandemic progresses and we see more remote working, virtual meetings and the cloud-based storage of information, the demand for data centers has continued to grow significantly. These data centers are getting built in traditional markets like Virginia, but also in markets in the Midwest, like in Ohio. There are a couple of large-scale data campuses getting started in Ohio right now. We are also seeing big demand for data center space in Boise, Idaho.
Then there is the advanced-technology manufacturing space. A lot of the demand for these spaces is driven by consumers’ habits when buying electronics. The semiconductors required to power these electronics are in high demand. We are also seeing the transition to electric vehicles. Those two things are resulting in an incredible demand for new construction space in this area. There are more than 30 large-scale advanced tech projects at around $1 billion either under construction or about to start in the country right now. Those are large-scale, billion-dollar capital investments per project that are under construction or are starting construction in the next six months.
And it doesn’t look like the transition to electric vehicles is slowing any.
Johnson: Not at all. You had the start-up companies like the Teslas in the mix early. Now you have newer start-ups. Like Lucid Motors. But the big thing that has happened, is that the big-three automakers have started their push toward electric vehicles. They are building their infrastructure out at a rapid pace. It is now a complete industry boom.
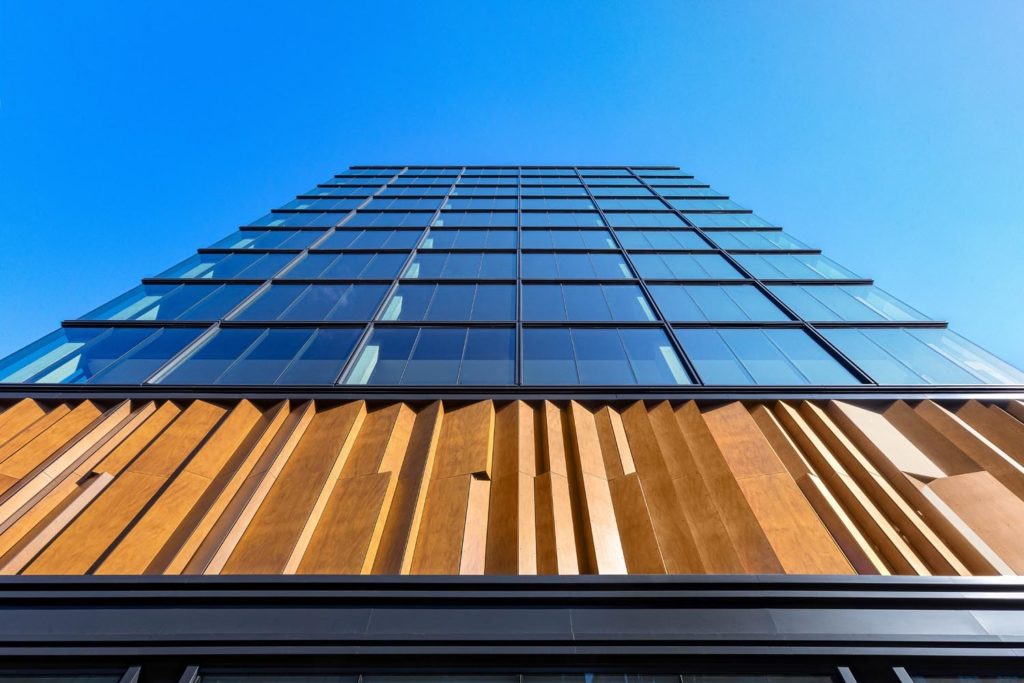
How about the office market? I know that has been a challenging sector across the country.
Johnson: We are very active in the office market. That, though, is the segment that the customers have put a pause on as people have worked from home. The investment market is trying to determine what the next phase of office growth is. They will start to figure that out soon. The large employers are starting to get their employees back to the office. Companies like Google and Apple have made their announcements. The fine print, though, shows that some companies are only requiring their employees to come into the office one day a week.
The key thing is to see how that evolves over time. How are employees going back to the office? We do have some larger clients that have already started talking to us about office projects in the future as they are anticipating getting their workers back. They are planning to fill offices again and need space in the not-too-distant future. That mimics with Clayco’s approach: We were very intentional about getting our workers back in the office as soon as possible in a safe way. We believe in collaboration People perform better when they are surrounded by their peers. They are more efficient in person than when working virtually. In the long run, I think that is how this will all shake out.
Read More: A story of soaring demand and rising challenges – REJournals